Die Fehlermöglichkeits- und Einflussanalyse (FMEA) ist eine wichtige Technik des Qualitätsmanagements für die Fertigungsbranche. Dabei geht es darum, systematisch potenzielle Fehlermodi in Produkten oder Prozessen zu identifizieren und deren Auswirkungen auf die Gesamtqualität zu bewerten. Durch die Priorisierung dieser Fehler nach Schweregrad, Häufigkeit und Erkennbarkeit hilft die FMEA Herstellern, kritische Probleme anzugehen, die Produkte und Prozesse beeinträchtigen könnten, und die Kundenzufriedenheit zu sichern.
In der Fertigung wird die FMEA sowohl während der Konstruktionsphase (Konstruktions-FMEA) als auch während der Prozessphase (Prozess-FMEA) angewendet. Die Konstruktions-FMEA zielt darauf ab, Fehler zu verhindern, indem Risiken in der Produktentwicklung vor Produktionsbeginn bewertet werden, während sich die Prozess-FMEA auf die Identifizierung und Minderung von Risiken im Herstellungsprozess selbst konzentriert. Dieser proaktive Ansatz ermöglicht es Herstellern, frühzeitig korrigierende und aufdeckende Maßnahmen umzusetzen, was die Fehlerwahrscheinlichkeit reduziert und einen reibungslosen Produktionsablauf sicherstellt.
FMEA-Softwaretools verbessern diesen Prozess, indem sie ein strukturiertes Framework für die Dokumentation und Analyse potenzieller Fehler bieten. Diese Tools erleichtern die Organisation komplexer Systeme, ermöglichen effiziente Risikobewertungen und unterstützen die Priorisierung von Korrektur- und Detektivmaßnahmen. Durch die Integration in andere Qualitätsmanagementsysteme gewährleistet FMEA-Software, dass alle relevanten Informationen zugänglich und aktuell sind, was Herstellern hilft, hohe Qualitäts- und Konformitätsstandards zu erhalten.
Verwandte Produkte: Opcenter X Quality | Teamcenter Quality & Compliance
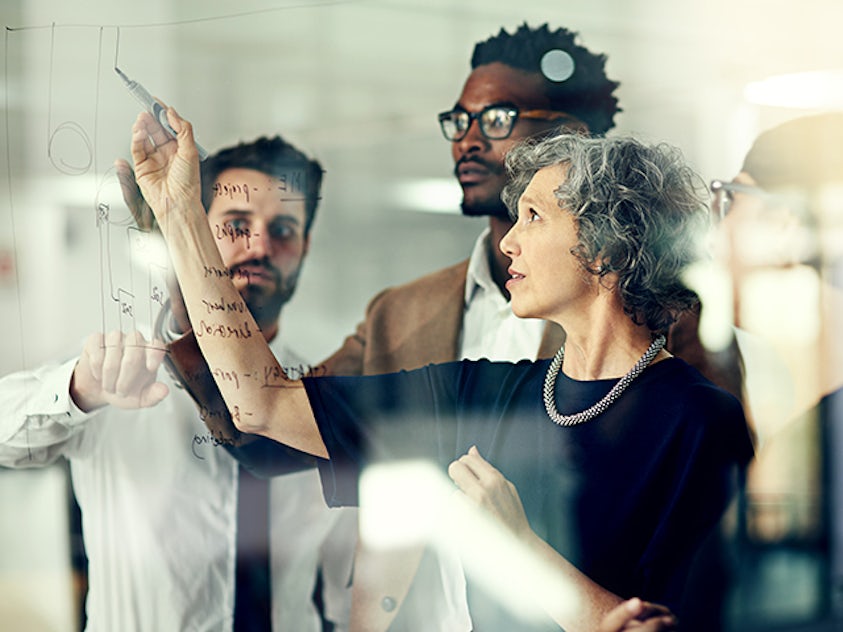