Crea y gestiona modelos de ensamble de cualquier tamaño y complejidad con las potentes herramientas de diseño de ensambles CAD. Al admitir técnicas descendentes y ascendentes, puedes gestionar y navegar por modelos de ensamble y lograr que tu equipo esté bien organizado y al día:
- Maneja complejos diseños de ensamble a diario
- Accede a estructuras de control y restricciones para ensambles paramétricos que simplifican los cambios de diseño y aceleran el modelado de configuraciones, opciones y variantes
- Diseña en el verdadero contexto del producto
- Valida tus diseños, identifica problemas y resuélvelos mediante maquetas digitales
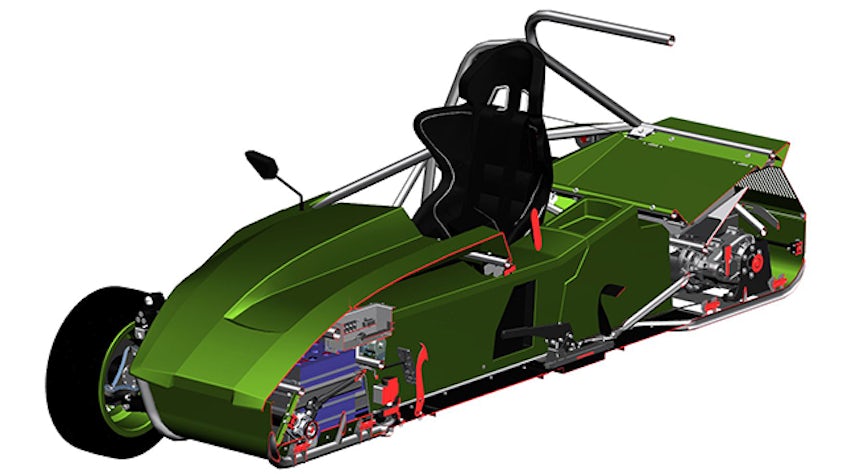