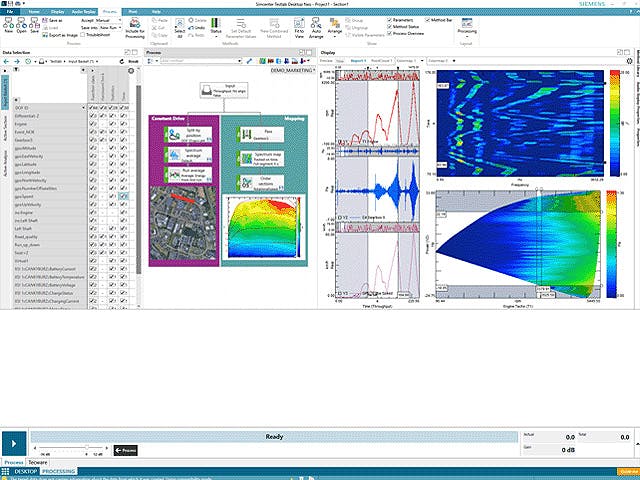
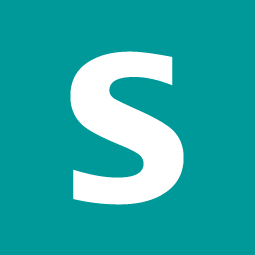
In response to the main market drivers – energy efficiency, safety and performance – many products now include controllers and electronic components that help optimize the product performance or refine its brand character. The widespread use of advanced control systems increases the complexity of product development, simulation and testing.
To accelerate system testing at any development stage of the model-based development process, Simcenter extends its portfolio with model-based testing capabilities. By integrating test and simulation in a single environment for validation of product performance, testing costs and risks can be reduced, productivity increased, and extra system insight gained. Model-based testing maximizes the consistency of used tools and methods while providing a highly agile mechatronic system engineering environment. It also enables attribute-specific evaluation using virtual models, combined virtual-physical models and physical prototypes.
This unique solution merges physical testing and simulation into one environment to accelerate development by providing augmented engineering insights.
Ensure results consistency of your simulated and physical testing analyses. Model-based system testing allows you to employ the same analysis methods and the same libraries and parameter settings, regardless of the origin of the data. Our solution gives access to simulated data from early engineering phases and enables analysis with data measured on physical prototypes. The analysis and processing methods applied simultaneously on measured and simulated channels yield unambiguous data sets.
Forget about file formatting, data import, time-base synchronization and unit conversion. Model-based system testing takes the burden away by running your simulation models inside Simcenter Testlab and by enabling model-driven data selection of multi-physical simulation results from Simcenter Amesim. The simulation data and simulation model exchange help to keep your results automatically organized and properly displayed for immediate correlation.
Easily include simulation models using the FMI 2.0 standard – alike system simulation models from Simcenter Amesim – in any analysis process in Simcenter Testlab Process Designer. Use test data as functional mock-up interface (FMI) model input data to simulate operational conditions. The FMI model outputs become available as additional virtual channels in a test data format to augment test data for better engineering insights, for example, when direct measurements are not possible. Connect FMI model outputs to all existing analysis methods in the active process.
Vehicle subsystem integration is the complex process of bringing together components and subsystems into one integrated system, ensuring they all work together as intended. With the growing number of product variants, discovering integration issues late in the design is simply not an option.