在编创设计数据以定义座椅装饰覆盖件(包括缝线、覆盖件材料、连接件和硬件)时,使用 Mastertrim 可以简化编创任务,促进 3D CAD 数字孪生的创建。
这样,您能够根据更准确的反馈快速进行更改,并在整个开发过程中有效共享信息。
借助 Mastertrim 提供的所需工具,座椅装饰工程师能够:
- 减少对物理原型的依赖
- 在设计、验证和制造开发流程中实现效率和准确性
- 更好地简化造型、设计和制造之间以及原始设备制造商 (OEM) 和供应链之间的协同与沟通
- 利用数字孪生在整个开发过程中有效共享信息
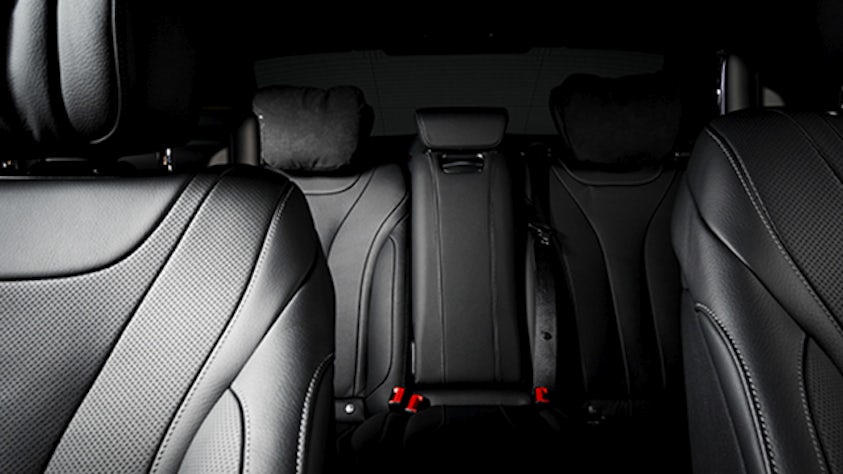
通过在 NX 中使用 Mastertrim,可以快速、高效地执行设计更改并在整个开发过程中共享信息。
在编创设计数据以定义座椅装饰覆盖件(包括缝线、覆盖件材料、连接件和硬件)时,使用 Mastertrim 可以简化编创任务,促进 3D CAD 数字孪生的创建。
这样,您能够根据更准确的反馈快速进行更改,并在整个开发过程中有效共享信息。
借助 Mastertrim 提供的所需工具,座椅装饰工程师能够:
Mastertrim Seat & Interior Design 的强大功能可以帮助您打造量身定制的解决方案。阅读下方有关这些功能的详细介绍。
简化下游工序并与制造车间和供应商有效沟通。
通过使用 Mastertrim,制造部门能够简化下游工序,并与制造车间和供应商有效沟通。Mastertrim 数字孪生增强了设计和制造部门之间对座椅装饰定义的沟通,使制造商能够识别皱褶等可生产性问题,并在制造原型之前将其传达给设计师。
使用 Mastertrim 在 2D 图样编辑和嵌套软件之间交换数据。格式化图样,以便在您选择的 2D 编辑软件中进行编辑。现有的 2D 展平图样可以导入 Mastertrim 中,然后进行编辑或用于测量面积、周长和长度,以及生成文档和成本数据(提供 2D 编辑应用程序和 Mastertrim 之间的双向链接)。这样可以将旧有数据引入数字孪生流程。
公司:SCS Interiors
行业:航空航天及国防行业, 汽车及交通运输行业, 船舶行业
位置:Duluth, Minnesota, United States
Siemens 软件:NX, SES (formerly Vistagy)