NX X Manufacturing Premium es el paquete más completo basado en la modalidad Advanced. Incorpora fresado simultáneo de 5 ejes y mecanizado rotatorio, junto con funcionalidades de fresado de 3 y 2,5 ejes, torneado y palpado en la máquina.
Funciones clave
Fresado de 5 ejes: las estrategias más recientes de trayectoria de herramientas proporcionan un control preciso sobre las operaciones. Además, permiten un mecanizado eficiente y seguro de componentes complejos en máquinas CNC multieje en una única configuración. Aprovecha el desbaste adaptativo de alta velocidad de 5 ejes para reducir de forma considerable el tiempo de mecanizado y mejorar la eficiencia general. Consigue acabados de superficies superiores mediante el acabado de curvas de guiado, que asegura la precisión en tus piezas. Utiliza el corte de virutas para aprovechar toda la longitud de la acanaladura y optimizar la eliminación de material y la vida útil de la herramienta. Aplica técnicas de fresado de tubos para maquinar con precisión figuras vacías y estrechas. Visualiza las características de la trayectoria de herramientas, incluidos los ángulos de avance, las posiciones del eje giratorio y las velocidades para mantener un mayor control y precisión durante todo el proceso.
Mecanizado rotatorio: optimiza las operaciones de fresado de 4 ejes con una entrada mínima, simplifica el proceso de mecanizado para una mayor eficiencia. Implementa avanzados controles para gestionar con precisión el desplazamiento del contacto de la herramienta y la densidad de puntos, lo que mejora los resultados del mecanizado. Automatiza el fresado de restos para asegurar que cualquier material sin cortar se mecaniza de forma eficiente.
Fresado de 3 ejes: acelera el mecanizado CNC mediante el uso del desbaste adaptativo 3D y reduce los tiempos de ciclo generales. Automatiza el fresado de restos para admitir el desbaste en varias etapas y asegúrate de que ningún material se queda sin cortar. Controla las regiones de corte con precisión utilizando métodos avanzados, lo que mejora la precisión de las estrategias de mecanizado. Emplea estrategias de acabado perfecto para ofrecer un acabado superficial de alta calidad.
Fresado de 2,5 ejes: mecaniza con fresado basado en volumen para posibilitar una programación más rápida de las piezas prismáticas y el mecanizado basado en figuras automatiza la programación. Las estrategias de mecanizado de alta velocidad pueden reducir el tiempo de mecanizado hasta en un 60 % y la programación de varias piezas aumenta la productividad.
Torneado: mecaniza con eficiencia piezas cilíndricas en máquinas de torno con husillos únicos y dobles mediante funcionalidades integrales de torneado. Las estrategias de desbaste incluyen operaciones de cara, torneado, torneado inverso, mandrinado y corte sesgado; por su parte, las técnicas de acabado abarcan estrategias de pasadas múltiples y refrentado. La perforación de agujeros incluye operaciones de punto, taladrado, punteado, viruta, escariado y roscado, con ranurado que ofrece un control flexible del punto de seguimiento y roscado para diámetros exteriores e interiores.
Palpado en la máquina: genera y visualiza trayectorias de palpado con palpado en la máquina. Crea eficientes ciclos de palpado para operaciones de fresado y torneado. Genera código de control numérico (CN) de forma impecable mediante un posprocesador integrado. Simula todo el proceso con un gemelo digital de la pieza, la sonda y la máquina herramienta. Detecta variaciones de proceso en tiempo real para ajustar los parámetros de mecanizado y obtener resultados óptimos.
Herramientas CAD integradas: NX CAM proporciona funcionalidades CAD líderes en la industria para el modelado, la edición y el ensamble, lo que acelera la programación CNC. Con los traductores integrados, puedes leer todos los formatos de datos estándar, como IGES, DXF, STEP, STL y JT.
Las métricas de fabricación se basan en pruebas internas de mecanizado o en estudios comparativos internos.
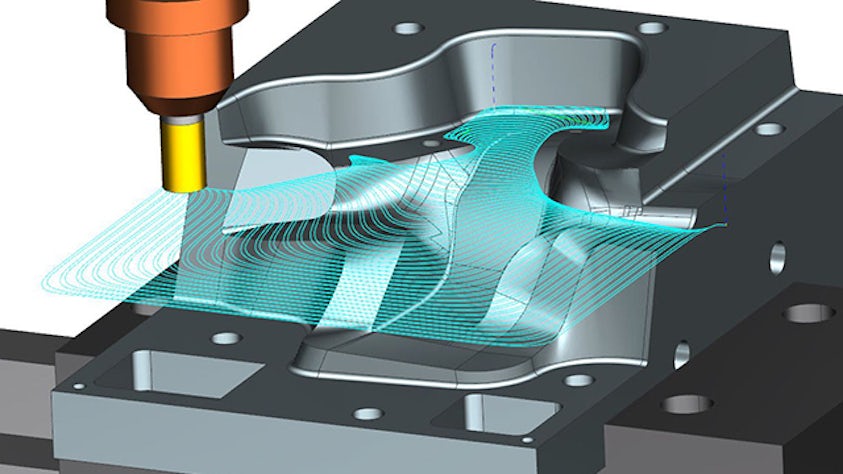
Ventajas de NX X Manufacturing:
- programa mediante avanzadas herramientas CAD/CAM adaptadas a tus necesidades de fabricación
- Reduce los costes iniciales y optimiza la implementación con tecnología en la nube
- Aumenta la productividad con funcionalidades de programación CNC líderes de la industria
- Mejora la colaboración entre las partes interesadas mediante soluciones basadas en la nube
- Amplía la funcionalidad de tus soluciones con Value Based Licensing
Solución personalizable
Amplía la funcionalidad con NX X Manufacturing Value Based Licensing para configurar y personalizar tus soluciones, entre las que se incluyen:
- Avanzadas herramientas de modelado
- Funcionalidades de mecanizado especializadas
- Simulación mediante código G
- Solución moderna de posprocesamiento