Supplier Quality Management is a systematic approach to evaluating and ensuring the quality of goods and services provided by suppliers. This process involves setting clear quality requirements and criteria that suppliers must meet and then regularly assessing their performance against these benchmarks. By doing so, manufacturers can identify areas where suppliers excel and where improvements are needed, fostering a culture of continuous improvement.
In addition to performance evaluations, Supplier Quality Management includes monitoring and documenting any quality issues that arise. This helps maintain a transparent and effective communication channel with suppliers, promptly address problems and reduce product failure risk. Overall, this approach not only enhances the reliability of the supply chain but also supports the strategic goal of delivering high-quality products to end customers.
Related products: Opcenter X Quality | Teamcenter Quality & Compliance
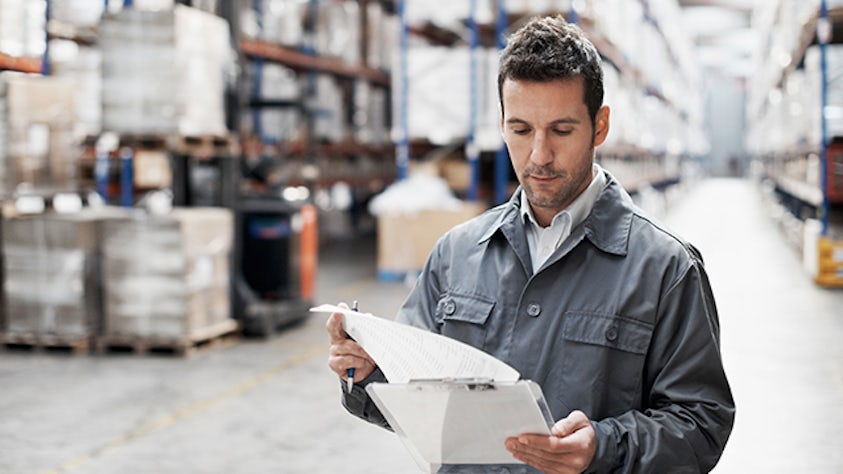