Rely on decades of expertise in structural testing and analysis for generating a modal model of your component or assembly to assess its dynamic behavior. This model can support you in product development phases, from specialized noise and vibration troubleshooting and benchmarking activities to design modification evaluation and CAE model validation.
Simcenter offers a powerful, flexible, yet user-friendly toolchain to extract modal parameters such as resonance frequencies, mode shapes, and damping factors based on impact and shaker Frequency Response Functions (FRFs), scaling up from small field-testing activities to high channel count modal survey campaigns in the lab. It leverages advanced modal identification techniques for increased prediction accuracy and fast estimation.
Our end-to-end solution for experimental modal analysis is tightly integrated into our dedicated hardware for FRF data acquisition and our software for 3D simulation to ensure a streamlined process from pre-test definition to instrumentation, testing, processing, and validation. The goal is to provide support throughout the complete process, providing engineers and designers with the right tools at the right time.
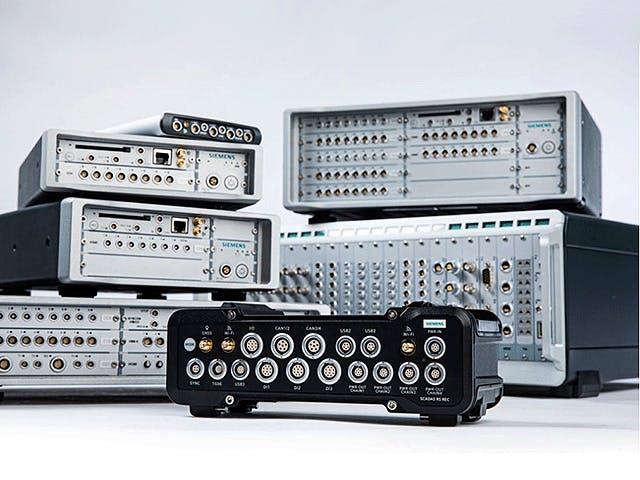
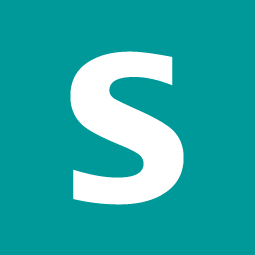
Simcenter
Simcenter SCADAS hardware
Gain productivity with a broad range of test data acquisition hardware for multiphysics measurement campaigns. Simcenter SCADAS includes portable mobile units, autonomous recorders and high-channel-count laboratory systems.