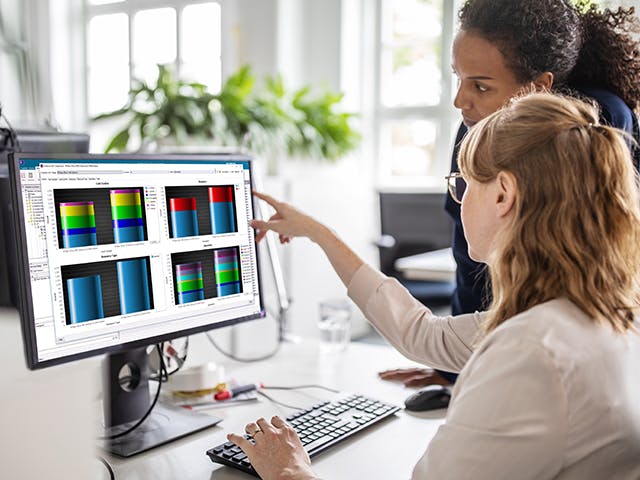
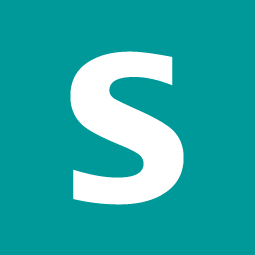
Wiring harness design engineers can effectively capture design intent to create fully detailed and validated harness designs rapidly and accurately.
Capital offers automated wire harness engineering, validation and reporting capabilities, enabling harness engineers to efficiently prepare product data.
Capital wiring harness cost modeling enables engineers to create comprehensive models that ensure realistic cost generation and accurate quotations.
Reduce new product introduction times by leveraging digital data continuity and intellectual property (IP) reuse. Optimize designs and improve product quality by applying automation and simulation with digital twin technology.