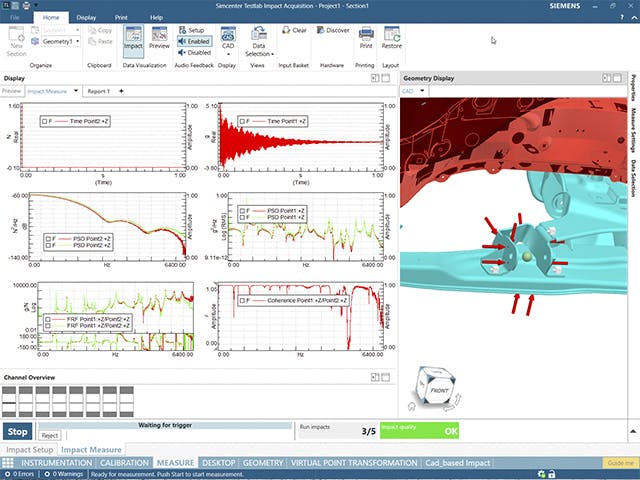
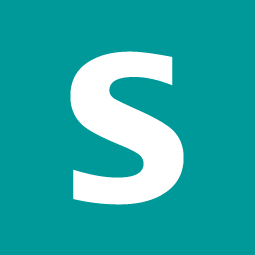
Certification and qualification of products require specific dynamic tests whereby external excitation – shock, vibration and noise – is applied. In these tests, excitation systems reproduce the realistic environmental conditions that products are subject to, such as shocks during transportation, vibrations during operation, or extreme launch conditions.
Our end-to-end solution for shock and vibration testing integrates an effective, high-speed multi-channel closed-loop shaker control system with parallel data acquisition and powerful analysis capabilities. It is a very intuitive tool for routine random, shock, sine, and combined modes testing. It features comprehensive time data replication applications, advanced functionalities for multi-axis vibration testing and acoustic field control, and is perfectly safe for vibration and acoustic qualification of space systems. Functionalities for test definition and analysis complement the offering.
Simcenter testing solutions provide a full suite for dynamic environmental testing of space hardware.
Our rack-based laboratory data acquisition systems combine expandable channel count with reliable high-speed throughput performance. Employ them for independent monitoring or to add multiple channels to an existing vibration controller. Our solutions record, analyze and reduce vibration, acoustic or shock data in real time, using the hardware configuration that best fits your needs.
Multi-axis vibration testing improves test efficiency as it simultaneously excites all vibration axes. It increases test confidence by applying realistic vibration environments. Our advanced multi-axis vibration testing solutions embed robust control algorithms to accurately replicate multiple time-traces or multiple power-spectra targets using several exciters.
Before launch, extensive testing is required to understand whether the vulnerable spacecraft can survive the intense acoustic loads under the fairing during launch and liftoff. Our innovative closed-loop control solutions allow you to confidently perform acoustic tests in reverberation rooms and direct field environments. It provides secure, traceable, efficient and smart control capabilities to ensure maximum hardware protection and to achieve the desired acoustic levels as specified in the launch vehicle manual.
Our dynamic environmental testing solutions embed a wide range of solutions for test definition and analysis. Define a realistic and accelerated test program to help reproduce field failures, perform shock response spectrum analysis to analyze shock data, or reduce vibration data of hundreds of channels using offline data reduction.
Vibration and shock testing helps engineers certify and qualify products, ensuring they properly operate under external conditions. Our intuitive vibration qualification testing solution provides accurate closed-loop shaker control for standard sine, random and shock excitation. It provides comprehensive capabilities for the replication of time data or combined tests. It is also scalable to engineering needs with powerful analysis tools to get more insights out of test data.
Thales Alenia Space partners with Siemens to explore new tools and methods for acoustic testing in the space industry. Their project delivered the unmatched performance of generating a 147 decibels direct sound field.
Firma:Thales Alenia Space
Branche:Luft- und Raumfahrt
Standort:Toulouse, France
Siemens Software:Simcenter 3D Solutions, Simcenter Testing Solutions