Reduce production time as NX readily creates information for harness manufacturing. Automatically create a flattened model of the wire harness that includes the electrical intelligence and details such as tie wraps, clips and grommets, and relative positions of connectors.
Manufacturers can use the flattened model as a reference for 3D jig design. Or, you can use NX to easily create accurate formboard drawings.
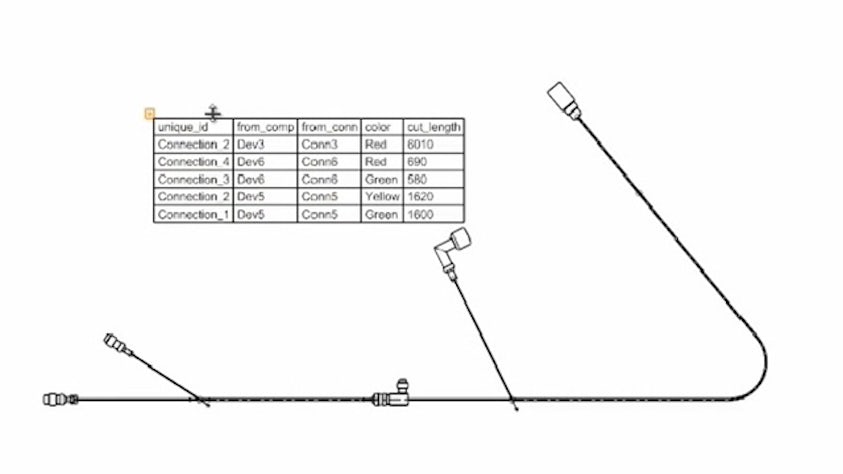