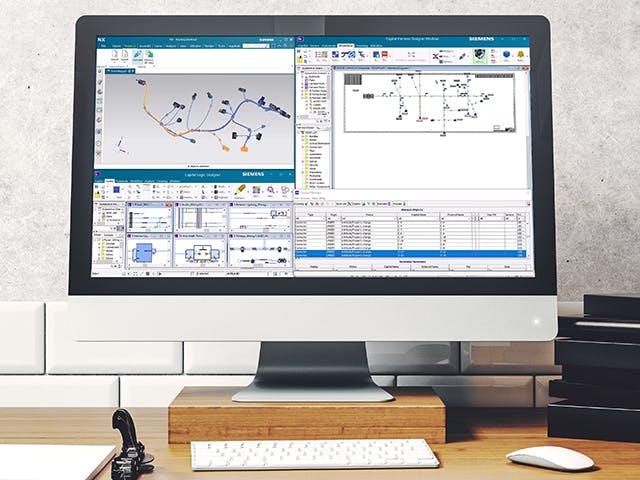
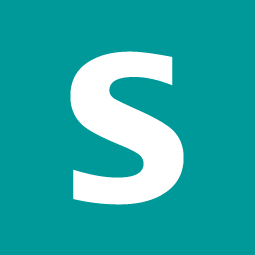
With Capital, formboard designers can create an optimized, ergonomic layout based on dynamic feedback of labor effort/times related to each component.
Use Capital to capture and apply best practice techniques to the wiring harness manufacturing process planning and cost estimation tasks.
The quality of manufacturing documentation is vital to minimize errors in builds. Create manufacturing documentation directly from engineered harness data and the defined assembly process sequence.
Leverage a digital twin with Capital to transform your company’s engineering, costing and manufacturing performance. Eliminate documentation errors, reducing creation costs and ultimately boosting profits.