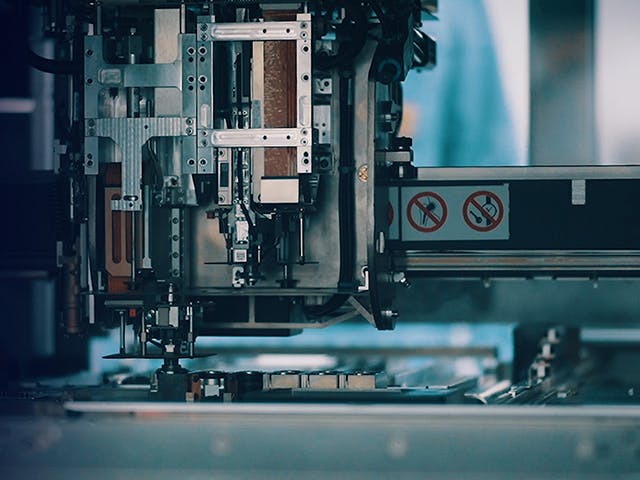
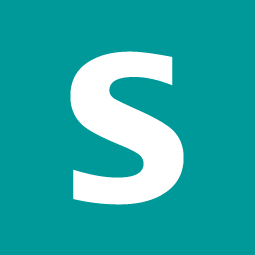
Opcenter Planning software considers forecast and long-term orders, supports feasibility decision making, and affects the general direction of production.
Advanced Planning is a powerful production and capacity planning system that helps you make strategic decisions about your factories, resources, and workforce.
Planning for Bill of Materials (BOM) can be expanded into its list of raw materials. The production plan for these items can then be calculated. Based on the BOM and the production plan, the proposed materials purchase requirements can be exported to an ERP system or Excel for action.
Replenish raw materials and component inventories to ensure production readiness and flow. MTO planning requires close coordination of the entire supply chain and an ongoing evaluation of future demand changes, including their effects on the manufacturing environment.
Generate accurate and achievable master production schedules (MPS). Consider the following: rough cut capacity, pack-forward figures, target days of stock cover, manufacturing preferences, minimum and maximum reorder quantities, reorder multiples, and product shelf life. Production capacity can be specified as a quantity, duration or weight.
Once an initial Master Production Schedule (MPS) has been created, data can be displayed as stock profile graphs and capacity usage graphs. The MPS can be changed by simply clicking and dragging a point on the stock or capacity graphs, and the production of a particular item can be moved from one planning period to another. Any changes made will be reflected in all the linked plot and grid windows.
Company:SUMIDA Group
Industry:Electronics & Semiconductor
Location:Lehesten, Germany
Siemens Software:Opcenter Execution Core
Seventh generation Intel Core i5 processor
16GB random access memory (RAM)
Double the amount of RAM for virtual memory (paging file size)
50GB disk space
Windows 10