Simcenter FLOEFD is a fully CAD-embedded CFD software with multiphysics capabilities, for designers to analysts. It helps shorten development by up to 65-75% compared to typical CFD approaches by frontloading fluid flow simulation and thermal analysis and using native CAD geometry.
Frontload CFD simulation to shorten development
Simcenter FLOEFD enables design engineers to perform simulation earlier in the design process when it is more cost-effective to identify and fix problems or explore improvements. Integrated in CAD, it has shown improved productivity by a factor of x2 to x40.
Leverage an intuitive CFD interface for designers
Put simulation in the hands of design engineers with the Simcenter FLOEFD CAD embedded interface, guided simulation set up and execution, intelligent automation technologies and straight forward viewing of results. Allow them to explore design performance earlier so they can make informed decisions without having to overcome traditional barriers.
Perform CFD directly on native CAD geometry and eliminate CFD overheads
Eliminate delays in geometry translation between tools and overcome complexity in preparing CAD geometry for CFD analysis. Simcenter FLOEFD uses native geometry directly: so as you explore performance or evaluate changes to a model, the CAD model is being changed concurrently.
It has key strengths in robust automatic meshing and unique SmartCell technology that enables handling of CAD geometry of any quality. These strengths help to handle small narrow gaps in assemblies and surface inconsistencies, which often cause long delays for healing in traditional CFD tools. This is complemented by intelligent automation for pre-processing, such as automatic sealing of CAD geometry and leak identification.
Use simulation driven design – explore, compare and optimize
Leverage parametric studies and design exploration functionality to evaluate more design options within the time available. Evaluate 'what if' scenarios to ensure product performance and reliability in different conditions.
Using this software, you can easily compare designs using side-by-side with CFD result visualizations, plots and tabular results and generating reports in just a few clicks. When your design is optimized using simulation, you can directly communicate the CAD model to other engineering functions.
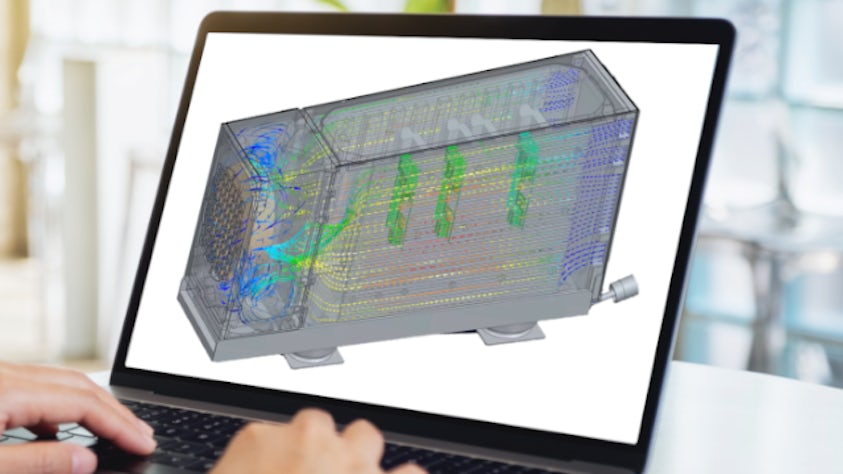
What’s new?
Explore Simcenter FLOEFD 2506 new features, including:
- Controlling sub-models: Project parameters
- Using multiple FMU based models in 3D CFD
- Faster Smart PCB and support within BCI-ROMs
- Transient structural analysis for thermo-mechanical studies
and find out the latest automation enhancements (EFDAPI) and much more