Whether it’s gases or liquids, Simcenter offers a comprehensive set of computational fluid dynamics models for single-phase flows. From compressible to incompressible, from laminar to turbulent flows, Simcenter provides CFD analysis for any flow regime. For turbulent flows, aerodynamics engineers across industries can choose from a comprehensive state-of-the-art set of turbulence models including all common Reynolds Average Navier Stokes (RANS) models, Detached Eddy Simulations (DES) and Large Eddy Simulations (LES).
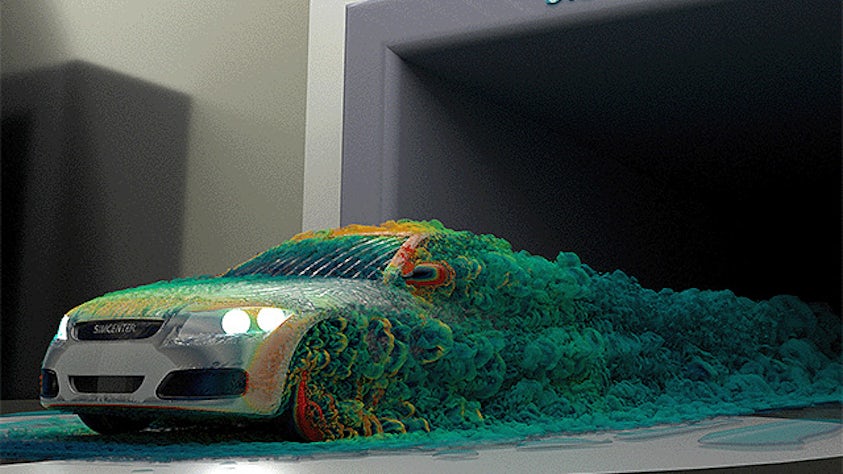