With more than 34 years of development and user feedback, Simcenter Flotherm is the leading electronic cooling simulation software solution for electronics thermal analysis. It shortens development at IC package, PCB and enclosure level through to large systems such as datacenters.
Accelerate electronics thermal design workflow
Simcenter Flotherm integrates with the electronics development workflow as a tool for thermal engineers to perform simulation and provide timely accurate results and feedback to other engineering functions. It supports thermal management, simulation-based decision making from early-stage architecture to final thermal design verification. This aids shortened development, and also helps to eliminate risks of costly reliability-related warranty costs or any late-stage re-spins.
Example capabilities that help engineers shorten the thermal analysis process include: innovative SmartPart technology, extensive libraries, EDA and MCAD data handling, a tailored and stable solver technology, state-of-the art compact thermal modeling techniques, automatic model calibration through to parametric analysis and optimization functionality.
Leverage accurate, fast thermal analysis
Leverage the Simcenter Flotherm instantaneous and reliable cartesian gridding that suits large complex electronics models with 1000’s of components, materials and powers. Simcenter Flotherm meshing and solver was designed from the outset to handle different length scales from sub-micron to meters. Furthermore, intelligent SmartPart based, object associated gridding eliminates the need for re-gridding as locations and orientations of objects are changed. This enables you to go faster and stay focused on simulation results and design space exploration.
Reduce model creation time with intelligent SmartParts
Use the Simcenter Flotherm thermal engineering-oriented interface, intelligent modeling and libraries to quickly construct models for fast, accurate studies to support early thermal architecture decision making. Build models quickly using SmartParts libraries of electronics specific components such as heatsinks, fans, enclosures, heat pipes and more.
Incorporate EDA and mechanical design data complexity during development
Enhance your model complexity and fidelity as EDA and mechanical design teams progress during development. You can import and pre-process CAD data. Handle EDA complexity by bringing in ECAD data for board routing and component layout information and modeling from all major EDA software file formats like ODB++ in a straightforward manner. Use the EDA Bridge for quick processing and options for appropriate modeling fidelity levels.
What's new?
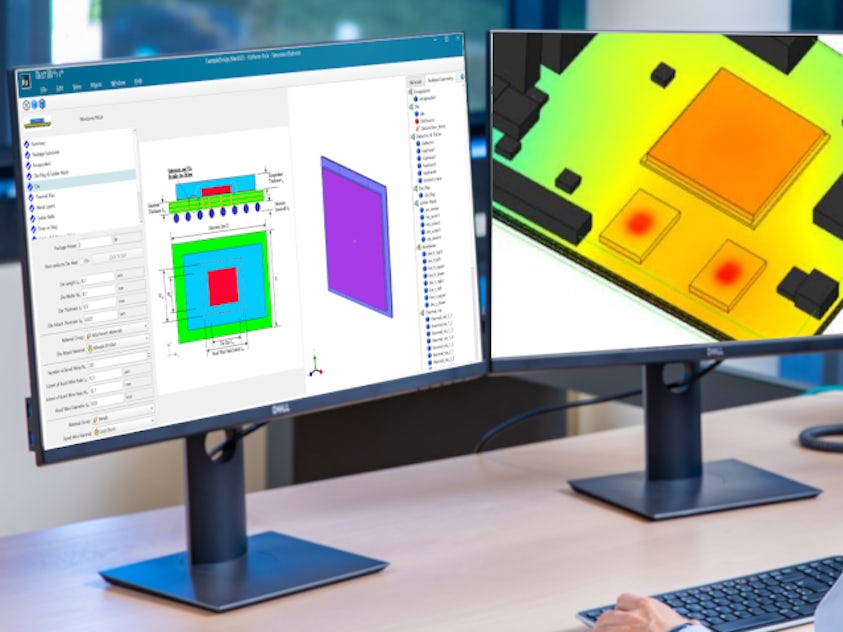
Learn about quick creation of detailed thermal models for common IC packages using the new Simcenter Flotherm Pack Module, two-resistor (2R) and DELPHI compact thermal model generation, and humidity modeling in Simcenter Flotherm 2504