The finite element analysis simulation process includes steps for model preparation, often called pre-processing, and results analysis, often called post-processing. Pre-processing steps include importing, defeaturing, and cleaning up CAD geometry, creating the finite element mesh, and defining loads and boundary conditions as well as solution parameters. Pre-processing is often the longest, most time-consuming step in the simulation process.
Simcenter can help you spend more time evaluating product performance and less time preparing your models. Quickly move from multi-CAD geometry data to a complete, run-ready analysis model using unique tools for CAE geometry editing, comprehensive meshing, finite element assembly management, multi-CAE solver environments, and fast simulation results post-processing and reporting. Quickly and efficiently pre- and post-process simulation models for accurate and fast simulation solvers so you can spend more time engineering innovation.
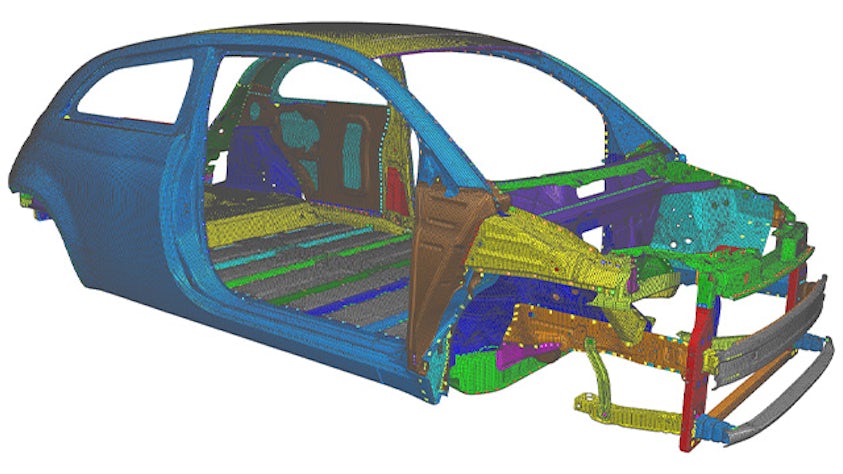