Unparalleled design tools
Leverage a complete parametric computer-aided design (CAD) system that enables you to work with non-uniform rational basis spline (NURBS), facet/mesh, and even sub-division bodies interchangeably and together in the same part. The robust design solutions available in NX mean you have all the tools necessary to design the simplest or the most complex printed parts.
Learn more about CAD in NX
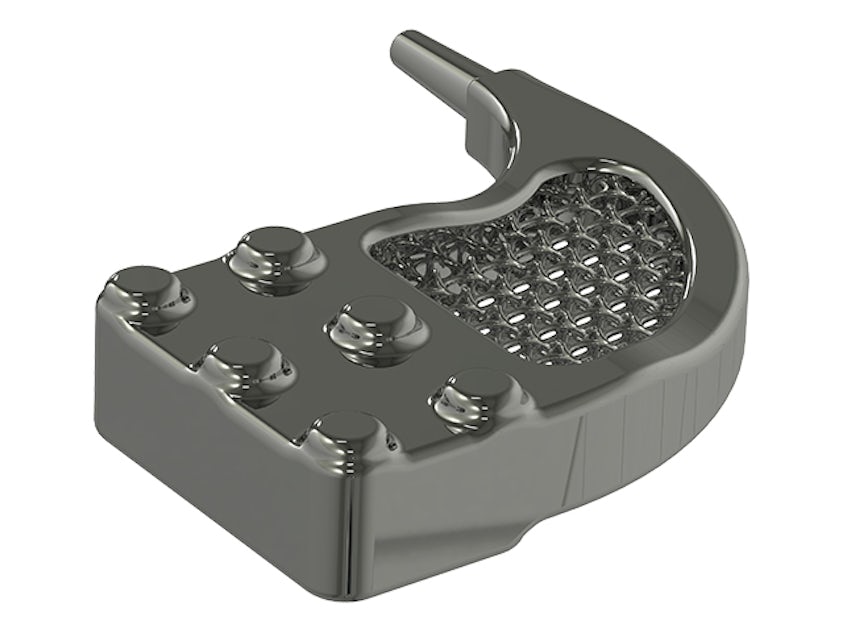