Automotive development teams need to know how the different noise and vibration sources from electrified and conventional vehicles will contribute to the overall NVH performance. They also need to deal with the increased engineering complexity across many vehicle variants while being under time and budget restrictions. But to do so, there is hardly any prototype available to test.
System NVH performance prediction is a robust solution that enables accurately predicting the interior and exterior NVH performance of any system at any stage of the development cycle. You can accurately create or assemble systems in a virtual environment using test and simulation data, easily evaluate the effect of modifications or components at different development stages and maximize the usage of all the data in the organization. The user interface is easy to use, allowing non-experts to predict the final product NVH performance accurately. Our solution allows your development team to deliver excellent NVH performance while keeping development times and costs under control.
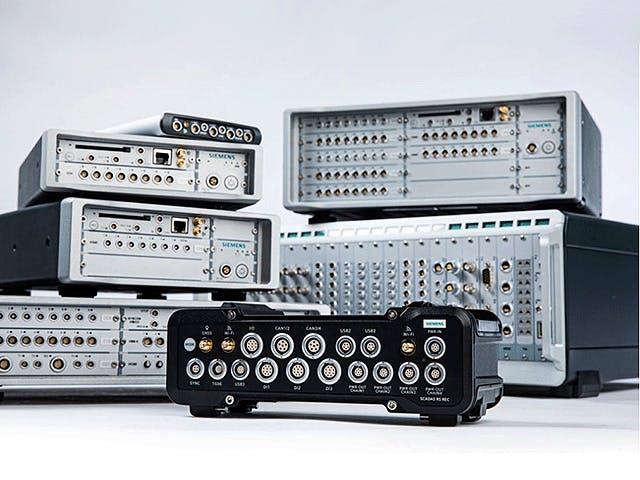
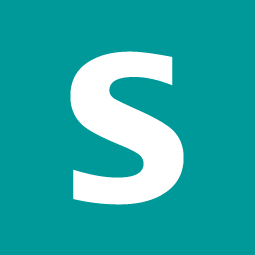